TWIP starts with the iron crystal structure
Pure iron exists normally in one of two main kinds of crystal structure: alpha-iron with a body-centered-cubic (bcc) lattice – forming a material known as ferrite, and a gamma-iron face-centered-cubic (fcc) lattice – forming austenite - see Figure 1.
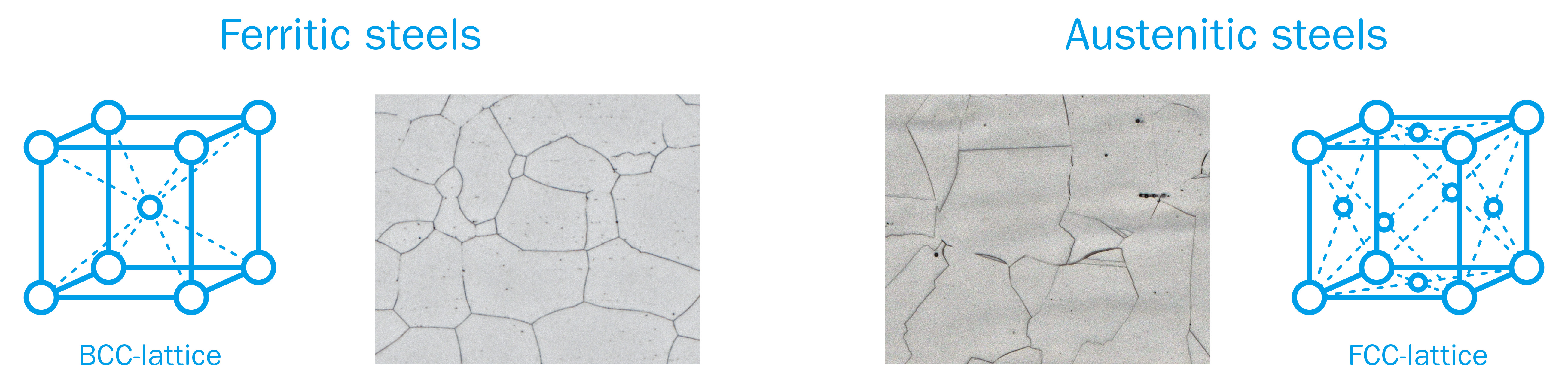
Figure 1. Pure iron can take on two crystal structures.
At room temperature, pure iron exists as ferrite. It transforms into austenite at temperatures above 911°C. However, special alloying elements called austenite formers - like nickel, manganese, cobalt or nitrogen – enable austenite to exist at room temperature. Because of their characteristic microstructure, austenitic steels show different properties than ferritic steels.
There is a further crystal structure that results in another material important in steel – martensite. The fcc structure of austenite that exists at high temperatures allows carbon atoms to fit easily into the spaces between the iron atoms. In contrast, there is much less space for carbon atoms in the bcc ferrite structure. If a hot steel is cooled very quickly (quenched), the carbon atoms become trapped in the ferrite. The result is a distorted crystal structure that forms martensite. This is important as martensite is very hard and is a significant factor in the strengthening of steel.
One of the main influences on the hardening mechanism of austenitic steels is the stacking fault energy (SFE), a material property at the atomic scale. The SFE is defined as the necessary energy to create a stacking fault as a two-dimensional lattice defect on a crystal face. A material with an SFE lower than 20 mJ/m² will form martensite during deformation – this is the TRIP-effect (Transformation Induced Plasticity). On the other hand, steels with an SFE between 20 mJ/m² and 30 mJ/m² can be characterized by a massive twinning effect called TWIP (Twinning Induced Plasticity).
TWIP hardening results from the creation of an increasing number of deformation twins in the austenitic microstructure, with the growing number of twin boundaries acting in the same way as grain boundaries to strengthen the steel. The TWIP effect also gives the steel a high instantaneous hardening rate (n-value) as the microstructure becomes increasingly finer.
TWIP steel advantages
TWIP austenitic stainless steels produced by Outokumpu are mainly alloyed with manganese (Mn) and chromium (Cr). The Forta H-Series comprises the Forta H500, H800 and H1000 grades – named according to their yield strength. The properties of these grades are shown in Figures 2 and 3.
Material | Yield strength Rp0.2 [MPa] | Tensile strength Rm [Mpa] | Elongation after fracture A80 [%] |
Typical values | |||
Forta H500 | 530 | 900 | 51 |
Forta H800 | 800 | 1000 | 31 |
Forta H1000 | 1000 | 1200 | 13 |
Figure 2. Forta H-Series’ mechanical properties.
The closely controlled addition of austenite forming elements gives TWIP steels a fully-austenitic microstructure. That means that the austenitic microstructure from the initial state remains stable throughout forming and metal cutting processes, deformation (such as in a crash impact) or welding, without transforming into martensite.
A key property of austenitic steels is that they are not magnetic. TWIP steels remain fully austenitic during forming and machining processes, such as drilling, turning and milling. Therefore, they are ideally suited for electric motor applications where it is essential to use non-magnetic materials to ensure maximum efficiency.
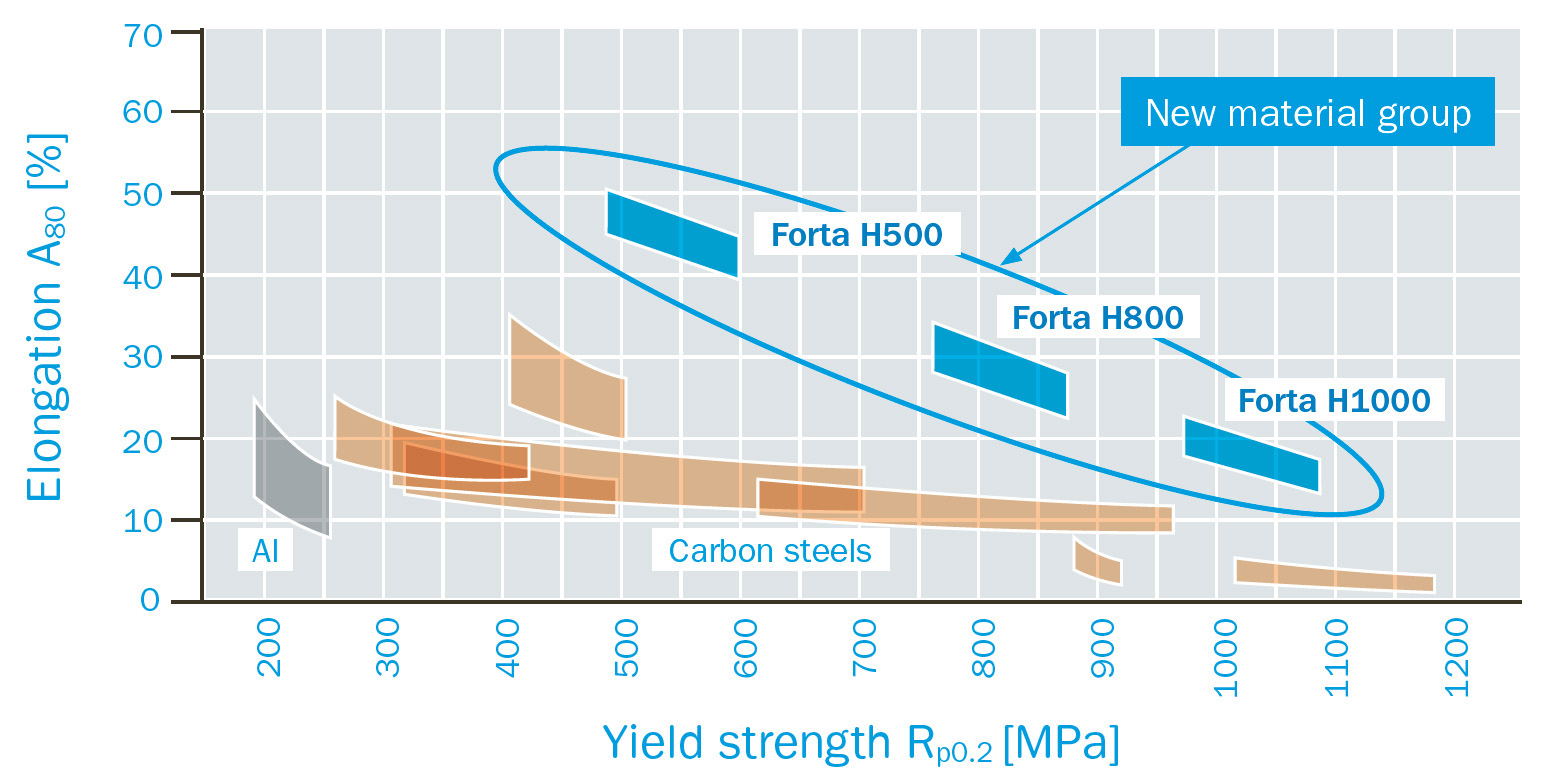
Figure 3. Comparison of Forta H-Series with other automotive materials.
During a crash impact, the Forta H-Series with its fully austenitic microstructure and the TWIP hardening effect demonstrates its full benefit: the material hardens in relation to the impact force, providing high resistance to the impact while simultaneously absorbing the impact energy. Simulations of structural elements, such as a b-pillar, show a direct lightweight potential of 35 % in relation to press hardened steels like 22MnB5, without brittle failure.
Figure 4. In a crash test at a speed higher than 30 km/h, Forta H1000 (on the right) absorbed the impact energy without failing. The test compared Forta H-Series to a hot-formed steel profile (22MnB5) on the left, which could not withstand the impact and suffered a brittle failure.
TWIP steels for the vehicles of the future
In addition to the direct possibilities for reducing the weight of existing designs, the Forta H-Series offers further advantages for designing new components, e.g. the reduction of needed components due to functional integration. Furthermore, this new material can enable the utilization of innovative geometrical degrees and forming processes to address weight and size challenges while also increasing component stiffness.