A quiet revolution is underway in cycling, with e-bikes being a comfortable, speedy, low-emission and low-cost way to travel. The European Cyclists’ Federation has forecast that e-bikes will account for half of the projected market of 30 million bikes by 2030. One challenge from having more and faster cyclists on the road is that good brake design is more important than ever before. Pasi Aspegren, Outokumpu’s Lead Technical Manager for mobility and transport, explains why stainless steel is ideal for brake discs and how to compare sustainability of material from different suppliers.
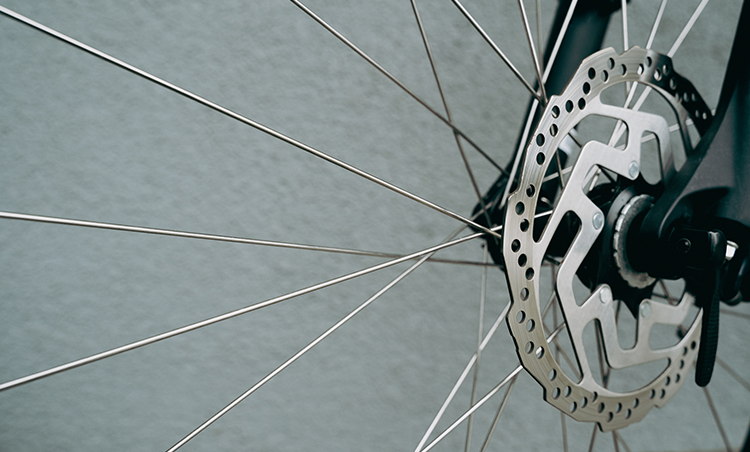
With their powerful braking in all weathers, disc brakes are the default for most bikes today. Stainless steel is ideal for the discs, which need to be lightweight and look good. In addition, high hardness provides wear resistance, while ductility ensures straightforward manufacture. In the longer term, high corrosion resistance and wear resistance help to maintain braking performance, as well as good aesthetics.
Stainless steel has all these properties, although it’s important to specify carefully as several stainless steel families and many grades provide different levels of performance as they have different microstructures and alloy content. Therefore, cycle component designers would probably choose different types of stainless steel for different applications on the same bike.
When it comes to brake discs, stainless steels with a martensitic microstructure such as Dura 4024 (EN grade 1.4024 standard) or Dura 420/4028 (EN 1.4028) are ideal. Heat treatment makes it possible to increase the hardness of the martensitic material to an optimal level to find a balance between wear resistance and ductility.
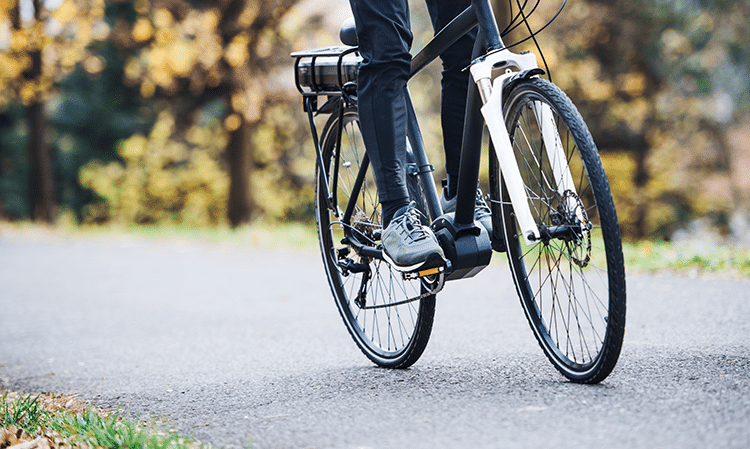
Manufacturing and material supply
For a brake disc producer, manufacturing efficiency is as important as a material’s properties. Components like brake discs are typically stamped out of flat sheet material, so manufacturers need a grade that is suitable for stamping, for example by meeting the required tolerance for flatness. Laser cutting is sometimes also used for prototyping and small production runs.
Choice of supplier is important, particularly in the current climate, where both pandemic and international conflict have disrupted supply chains. Original equipment manufacturers (OEMs) can reduce risk of delivery issues and protect quality by working with a well-established producer like us, with production sites and distributors around the world.
We are able to deliver a steady stream of high quality martensitic stainless steel material suitable for brake discs, chain rings and other bike components. As a result, bicycle manufacturers can rely on our support as they upgrade brake discs for better stopping performance and sustainability.
Energy and embedded CO2
Sustainability is becoming more important as a decision-making factor for buyers. It should be considered across the full lifetime of a product, taking account of the energy required to manufacture and repair the bike and its components. As a durable material, stainless steel makes components that last over a long life, which helps to minimize the overall carbon footprint. It is also recyclable at the end of its life.
Bike manufacturers can compare the carbon footprint of bike components using the ISO 14040 environmental management standard as a framework. It calculates the total carbon footprint of a product by combining the total of three scopes.
- Scope 1 is the direct emissions – in the case of a bike manufacturer, this could be gas burned during welding or heat treatment.
- Scope 2 covers indirect emissions, such as the emissions required to generate the electricity that runs the production machines. This figure varies, depending on the local electricity mix.
- Scope 3 covers the carbon dioxide emissions embedded in the raw materials that the bike manufacturer buys in. This area requires care to ensure that the business is comparing like with like, for example by demanding that raw material producers are also reporting their footprint under all three scopes according to ISO 14040.
To support these calculations, producers of materials such as stainless steel are now providing Environmental Product Declarations (EPDs). They help buyers compare products on an equal basis, and identify hidden carbon costs.
In some cases, engineers may want a quick estimate to compare different stainless steels’ carbon footprints. This can be done by comparing the recycled content. As a rule of thumb, the higher the recycled content, the lower the carbon footprint. That is because it takes more energy to mine and process virgin ore than it does to recycle existing material. Therefore, the more recycled content in a stainless steel, the lower the carbon footprint. At Outokumpu, more than ninety percent of our production is based on recycled scrap material, the highest level on the market.