Why is it important to know the ferrite content in duplex stainless steel?
Duplex stainless steel grades have a ferritic-austenitic microstructure, with a phase balance of approximately 50% ferrite and 50% austenite. They combine many of the beneficial properties of ferritic and austenitic stainless steels. The duplex microstructure contributes to the high mechanical strength and high resistance to stress corrosion cracking. Knowing the fraction of each phase present in the steel is vital in establishing that the material will have the desired properties.
What are the methods for measuring ferrite content?
There are a number of methods that have been developed over the years to measure the ferrite content in duplex stainless steel. Metallography is the oldest and most well- established. This can include: Point counting (PC) to ASTM E562 and Image analysis (IA) to ASTM E1245. There are also the diffraction techniques, most suitable for use as reference methods including X-ray and electron backscatter diffraction (EBSD) in a scanning electron microscope (SEM). One approach in the field, is to use the magnetic properties of the material, since ferrite is magnetic and austenite is non-magnetic. Examples of this approach include the MagnaGage (a calibrated magnet that measure magnetic attraction) and ferrite scopes which measure the permeability.
The ferrite scope
The ferrite scope, as shown in Figure 1, uses induction to measure the magnetic permeability of a material – its ability to support the formation of a magnetic field. The hand-held device is easy to set up and use. The operator simply has to place the probe on the surface of the specimen, the reading in terms of the ferrite number (FN) is displayed automatically and stored in the instrument.
Even if the method in itself is robust, there are a number of different factors that can have a significant impact on the reading obtained. These include:
- Curvature
- Thickness
- Surface condition
- Cross-section
- Chemical composition
- Deformation/stress
- Phase transformation – as unstable austenite may transform to martensite
- Structure, including texture and lamella thickness
It is important therefore, to establish your own references that are specific to the production procedures used. The measuring procedure must also be consistent so that the same cross-section and position are always measured.
As shown in Figure 2, the output from the ferrite scope can vary significantly according to the cross-section measured.
Figure 3 shows that there is also a different response for different alloys, with a difference of up to 5% between the measurement produced by image analysis and the ferrite scope.
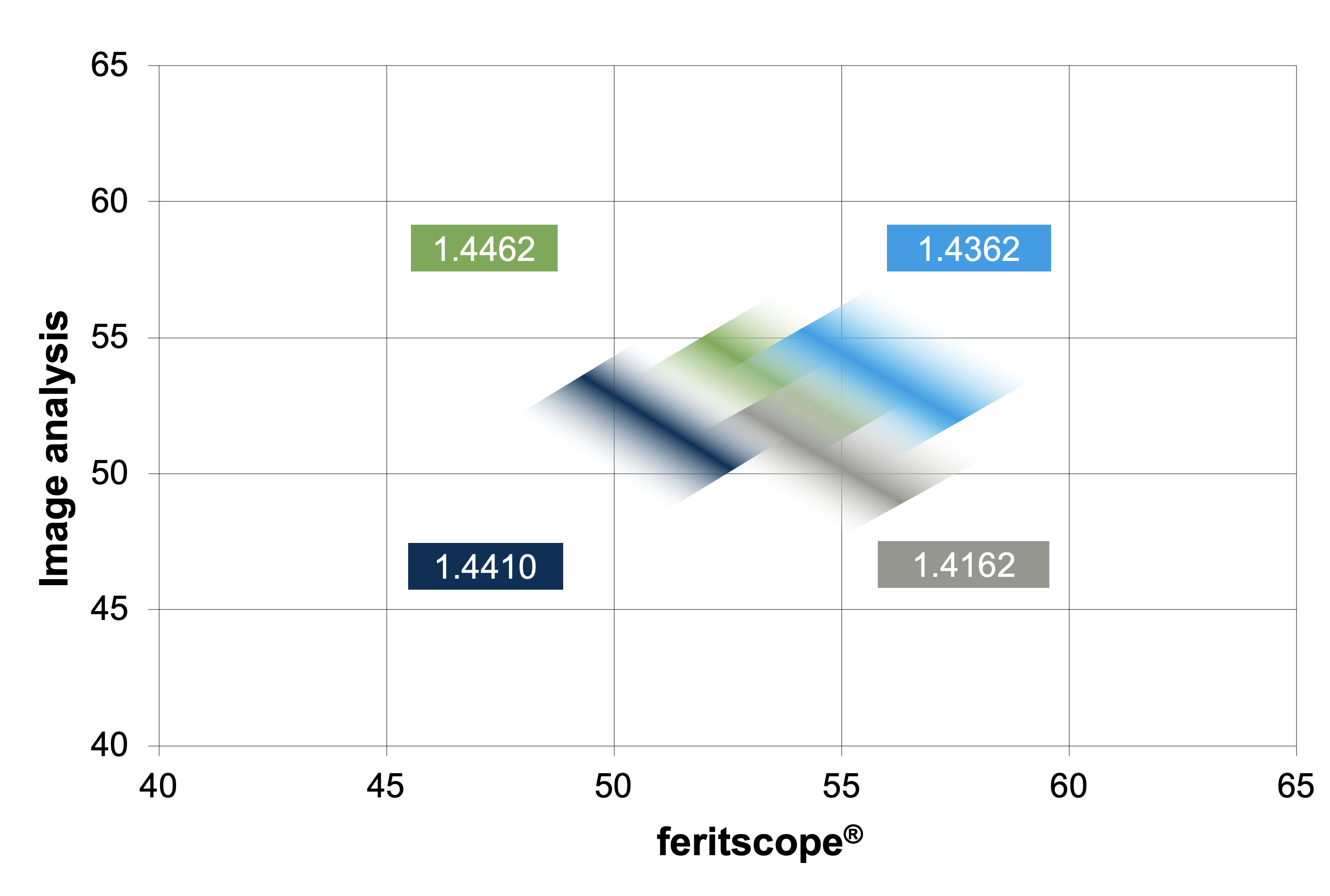
Main considerations when using the ferrite scope
The main considerations when using a ferrite scope are:
- Different products may give different measured values, so rolled material may differ from cast or welded material
- Different chemical compositions may give different responses
- For a rolled material, different measured sections and locations in the section can give different responses
- Values of up to 20% lower than the actual ferrite content can be found on a surface section for rolled products in the final condition with a perfect microstructure
- Induced deformation and/or stress will give a lower response
Suggested measurement procedures when using a ferrite scope
- Produce a reference line based on data from the instrument producer
- Produce a calibration offset based on specific products and a thickness factor if relevant
- Use consistent measurement procedures
- Expect bigger variances for thin materials
- Where possible perform cross-reference measurements with EBSD