Weight savings up to 40%
Forta H-Series offers a unique combination of high yield strength and high elongation to fracture made possible by its TWIP (Twinning Induced Plasticity) strengthening mechanism. The harder its pushed, the stronger Forta H-Series stainless steel becomes. This work-hardening capability makes it ideal for safety critical structural vehicle components, where it can also help to save weight. The indications are that for a body in white (BIW) manufactured normally in mild steel, a switch to Forta H-Series could result in a weight saving of up to 40 %. The new material is available as Forta H500, Forta H800 and Forta H1000 grades – the numbers refer to the yield strength of each grade.
Material | Yield strength Rp0.2 [MPa] | Tensile strength Rm [Mpa] | Elongation after fracture A80 [%] |
Typical values | |||
Forta H500 | 530 | 900 | 51 |
Forta H800 | 800 | 1000 | 31 |
Forta H1000 | 1000 | 1200 | 13 |
Table 1. Forta H-Series grades.
Enhancing crash performance
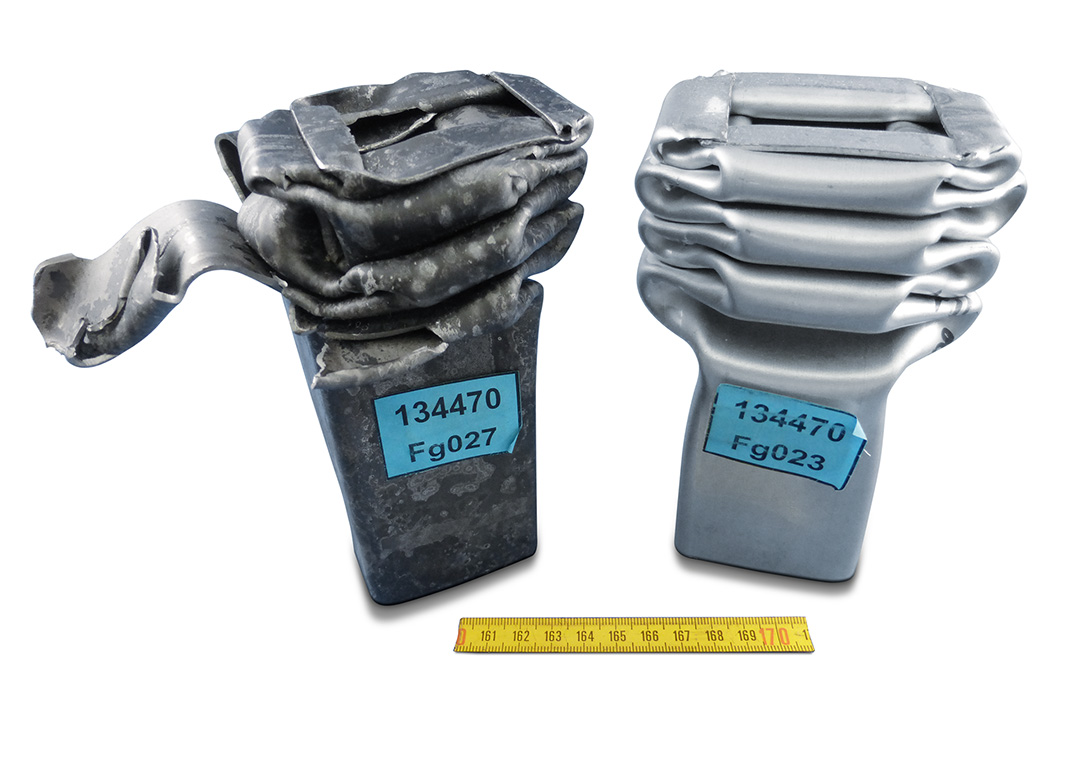
Image 1. Forta H-Series (H1000 on the right) offers greater energy absorbing capability than conventional steel (22MnB5 on the left).
Forta H-Series shows great potential for reducing the thickness of critical structural components while enhancing their crash performance. This is demonstrated in image 1 that shows test results from a crash at a speed higher than 30 km/h. The hot-formed steel profile could not withstand the impact and suffered a brittle failure. The Forta H1000 profile absorbed the impact energy without failing while the ductile welded areas allowed the transmission of the crash energy to the surrounding areas.
No need for coating
Because Forta H-series is a stainless steel there is no need for any coating such as electrolytic zinc coating or galvanizing. However, for exterior components it does need to be painted with a cathodic dip coating (cdc) in the manufacturing process. A specific benefit of Forta H-Series is its significantly reduced free electrochemical potential. It is suitable therefore for use with dissimilar multi-material parts like a car body - with no increased risk of galvanic or contact corrosion.
Ready to switch now
Forta H-Series is available in industrial quantities in thicknesses between 0.5 mm and 4.0 mm and in widths up to 1,250 mm. The material has been successfully approved according to the relevant automotive standards and is already in use in series production.
In many cases, Forta H-Series will be a direct replacement for existing steel materials. However, some adjustments to process parameters will be required and Outokumpu’s expert team is available to provide guidance on how to get the best out of the new material. This support extends from the earliest concept stage through to volume production and beyond.
One specific production advantage of Forta H-Series is that it achieves its properties by strain hardening during cold-forming. This removes the need for hot-forming, saving production complexity, cost and CO2 emissions during the manufacturing process.
Improved fire-resistance for e-mobility applications
Forta H-Series retains its fully austenitic non-magnetic microstructure even after forming or welding. That makes it ideal for electric motor components such as shafts and shrouds. It also has the added benefit of offering high strength properties at temperatures up to 300°C.
The new stainless steel grade facilitates the design of light, crash-resistant and cost-effective battery compartments to house lithium-ion (Li-ion) battery packs in electric vehicles (EVs). The key factor in this application is heat resistance in case of fire, where the general requirement is to contain a fire for up to 10 minutes to enable the safe evacuation of vehicle occupants. Aluminum materials used in first generation battery compartments fail after only five minutes at 600°C. In contrast, Forta H-Series, together with Outokumpu’s other austenitic grades, has survived testing at 1250°C for over 10 minutes with only a small deflection. And tests are ongoing to confirm its resistance to even higher temperatures.
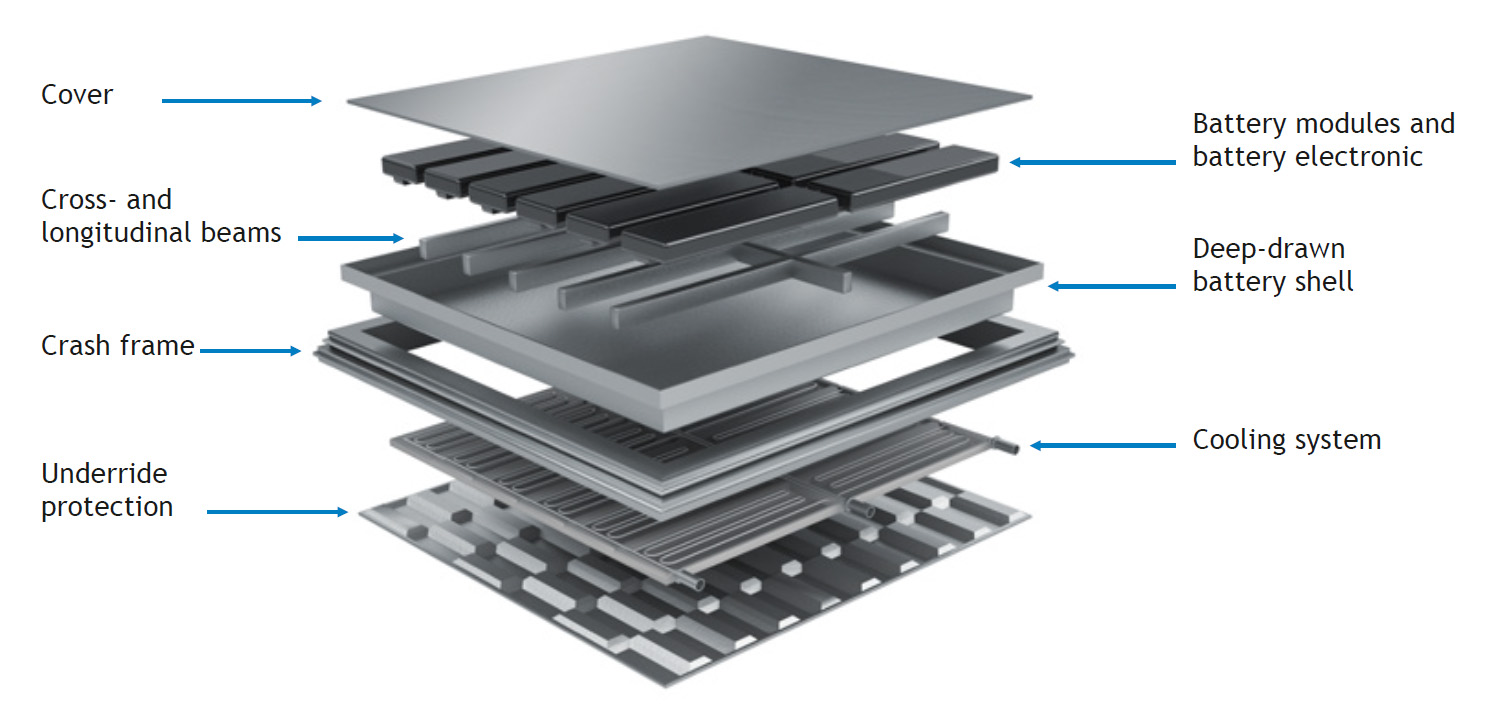
Image 2. Outokumpu stainless steel concept for an EV battery compartment.
Helping reduce CO2 emissions
Manganese-chromium materials are extremely durable and 100 % recyclable. Compared with aluminum and carbon steel, Forta H-Series contributes to a reduction in CO2 emissions over its total lifecycle. This is because using less material results in 30-40 % less energy consumption in production. Low weight results in lower fuel consumption and a decrease in CO2 emissions per kilometer.
Furthermore, stainless steels like the Forta H-Series, which are manufactured by Outokumpu with a recycling content significantly higher than 85 %, can decrease substantially the carbon footprint over the complete automotive supply chain. As the world’s first stainless steel manufacturer, Outokumpu publishes environmental product declarations (EPD) for its main stainless steel products.
The case for Forta H-Series stainless steel
Enhanced performance- High strength, lightweight material
- Excellent crash resistance
- Good corrosion resistance associated with stainless steel
- Suitability for use in multi-material construction with no risk of galvanic or contact corrosion
- 100% recyclability
- Easy to use as a replacement material for standard steel – often with only a readjustment of process parameters required
- Elimination of hot forming
- Structural parts/body in white
- Engine components
- Battery compartments
- GDI (gasoline direct injection) systems
- Seat structures, steering columns and dash cowls
- Channels, pillars and bumpers
- Global supplier for the automotive industry for decades
- Worldwide availability
- Deep understanding of the automotive industry and its supply chain
- State-of-the-art research and development centers
Forta H-Series is very versatile. But it may not always be the perfect choice for your specific application. However, the ideal solution will probably be found in Outokumpu’s broad portfolio that includes: HyTens – which is proving its capability in fuel tanks and head gaskets; Deco grades – for applications requiring special surface finishes, such as trim parts; Therma grades – for exhausts and other high temperature applications; Duplex grades – for high strength, and also ferritic grades.
Are you interested to learn more?
Recently, Outokumpu's Lead Technical Manager, Stefan Lindner, presented the properties and benefits of the Forta H-Series for automotive engineering as part of the Outokumpu Mobility Webinar Series. The recording is available on our website: "How stainless steels help to shape the future of the automotive industry".